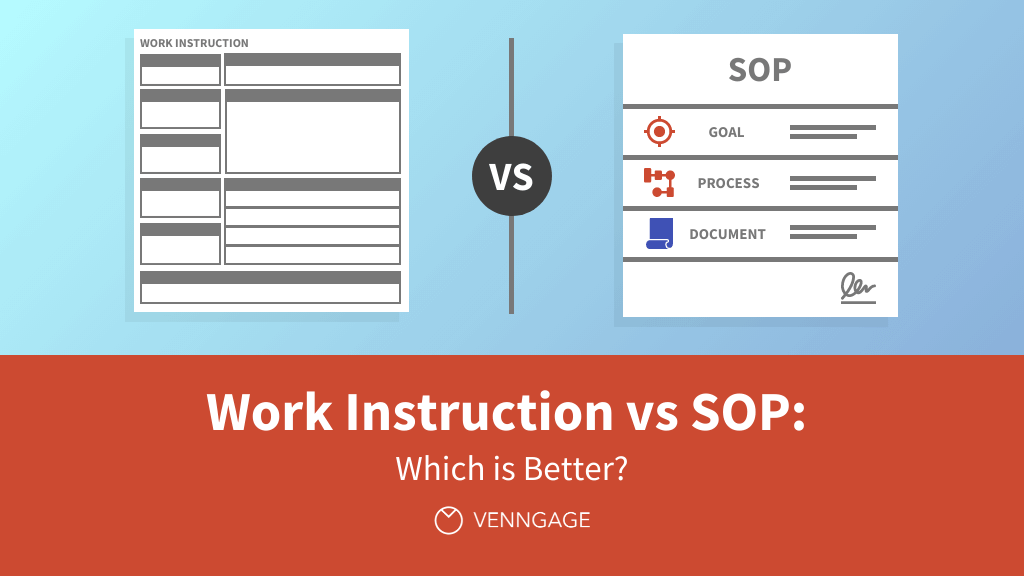
Work instructions and standard operating procedures (SOPs) are both process analysis tools used by businesses to make a process more detailed and actionable.
They ensure the proper and efficient accomplishment of tasks that make up core processes and key operating activities in a company.
In this article, we will define each term extensively to see the similarities and differences between them and figure out which one will be the better fit for your organization.
You will also learn how you can create work instructions and SOPs with Venngage’s checklist templates. Ready? Let’s get started!
Click to jump ahead:
- What is SOP?
- What is a work instruction?
- Difference between work instructions and SOPs
- When to use work instructions vs SOPs
- FAQs
What is SOP?
To provide a clear definition of an SOP (a standard operating procedure), we must first differentiate a process from a procedure.
A process is a series of actions or steps taken to achieve a particular result, while a procedure communicates the specific way to carry out a process. This means that a procedure is a more detailed version of a process.
Now, a standard operating procedure or SOP is a formal documentation of a procedure or routine activity in an organization. It provides general information about the activity and focuses on specifying details such as the people and resources needed to complete it.
Standard operating procedures outline:
- What the activity is
- Who performs the activity
- When the activity is performed
For example, this SOP checklist template identifies blog publishing as the activity, and the content writers, editors, and content managers are the people involved.
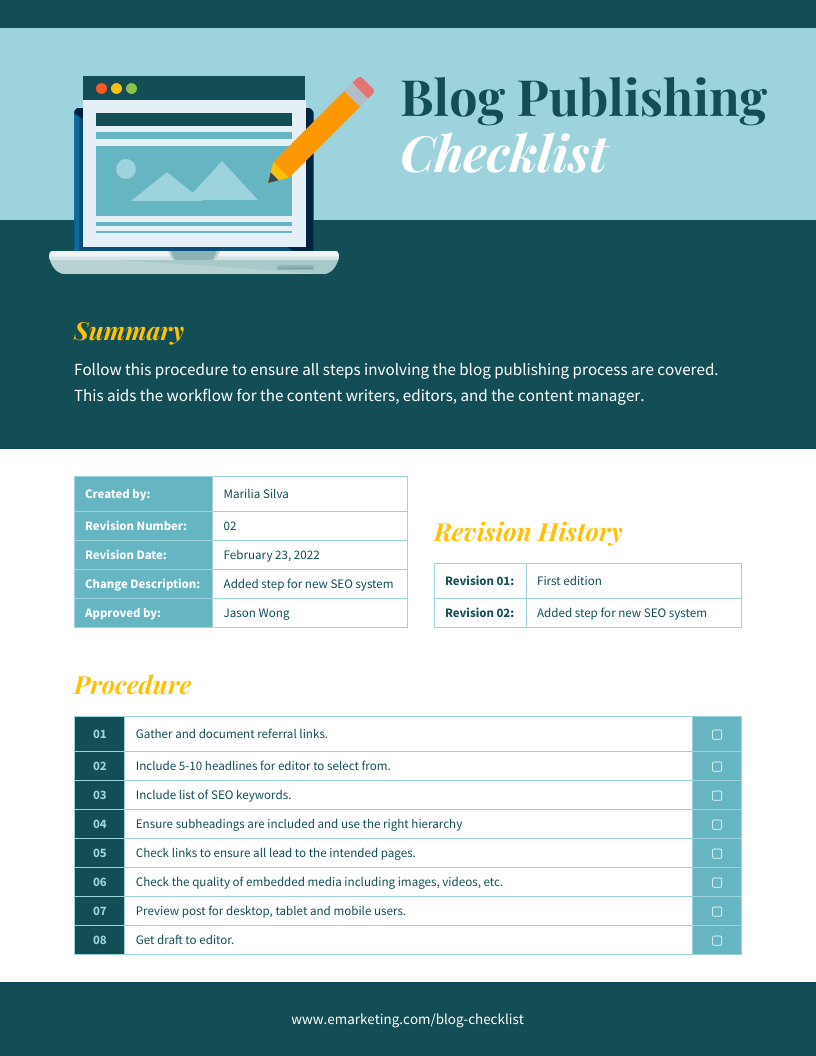
Who needs an SOP?
Standard operating procedures are assigned to different departments or business units to maintain and comply with industry regulations and business standards.
Managers can use SOPs to coordinate and assign target outputs and measure individual performance. At the same time, SOPs produce guidelines that employees are required to follow for consistency and efficiency.
What are the use cases for an SOP?
Standard operating procedures cover the processes, policies, and standards that keep an organization running. They can be used for various purposes, including:
- Documenting processes or establishing strict schedules and specific procedures
- Onboarding new employees
- Controlling product or service quality and consistency
- Simplifying performance management
- Guaranteeing compliance to standards and regulations
For example, this SOP documents the 7 steps involved in the talent management process for a company:
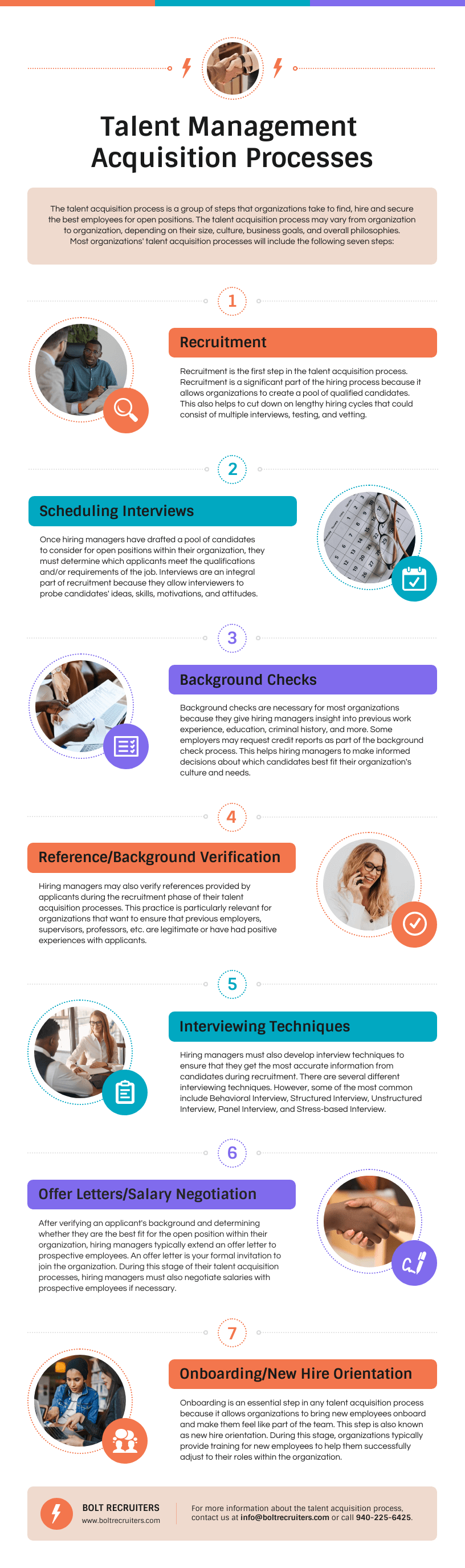
What is included in an SOP?
There are no official guidelines on how to prepare an SOP. However, a standard operating procedure checklist generally consists of 3 primary elements:
- A title that clearly identifies the procedure or activity
- The procedure, which includes its purpose, scope, requirements, and summary of its steps
- A checklist of activities for quality control and quality assurance
Here is an example of an SOP checklist for a cleaning job. As you can see, it contains a checklist of steps and activities that are part of the process of cleaning and practicing health and safety protocols:
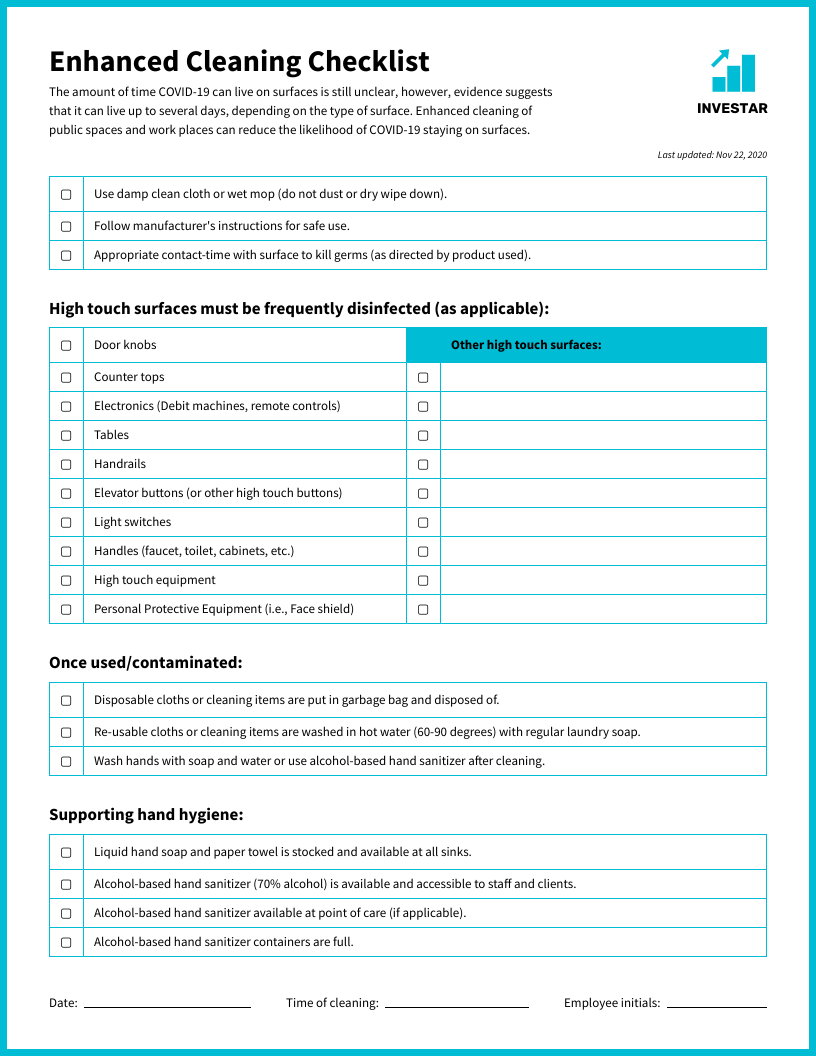
What is a work instruction?
On the contrary, work instructions are documents that contain very specific instructions or directions on how to carry out a certain task.
A work instruction explains and describes in detail the steps required to complete a task and how to do each step correctly.
This example shows the step-by-step instructions for responding to a negative customer review:
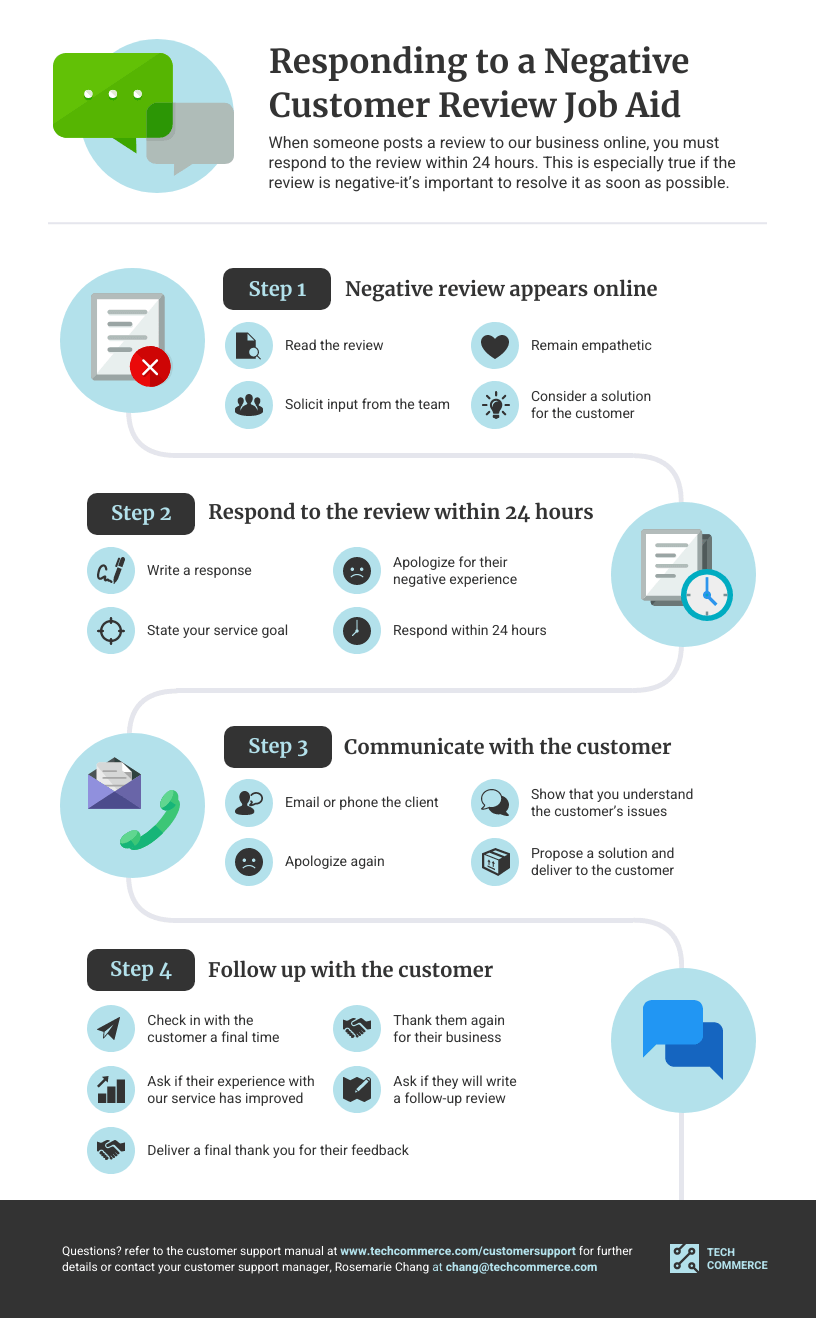
Work instructions focus on the instructions of the actual work or task at hand. They usually involve the participation of one person with one role in a single business unit.
In contrast, standard operating procedures can consist of more than one task and therefore include multiple work instructions and involve various roles and departments.
Who needs a work instruction?
Workers in highly controlled environments need detailed work instructions to help guide them in doing their jobs safely, accurately, and efficiently.
Work instructions can also help management teams ensure that the best possible means of accomplishing a task is clearly communicated and executed.
Once implemented, both work instructions and standard operating procedures become mandatory methods and guidelines in the workplace.
What are the use cases for a work instruction?
While SOPs are in charge of the ‘what,’ ‘who,’ and ‘when,’ work instructions answer the ‘how’ in a procedure. They ensure the successful completion of tasks that make up the daily operations of a business. Aside from that, they can be used for:
- Minimizing risks and errors
- Standardizing and streamlining workflows
- Resolving issues
- Promoting workplace safety
- Improving processes
For instance, this example contains an in-depth guide with complete steps on how to use an employee management system to streamline the process of clocking in and recording transactions.
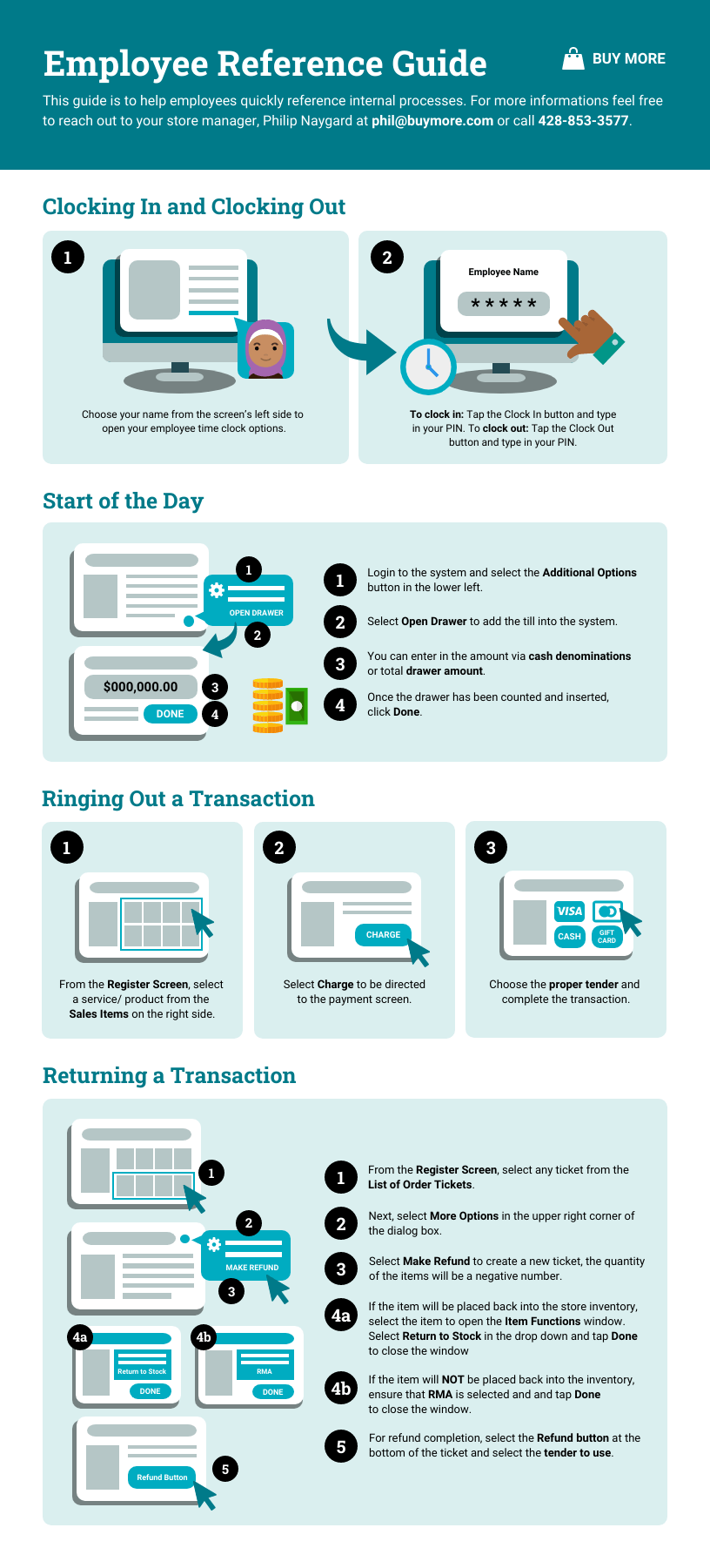
What is included in a work instruction?
There is also no standard way to create work instructions. Although they are more detailed than SOPs and have elaborate components, they can usually be compressed to less than one page that discusses a task’s…
- Title and description
- Objectives
- Purpose
- Scope
- Requirements
- Complete step-by-step instructions
- Expected outcomes
Here’s an example of a work instruction to help employees learn to use Google Meet:
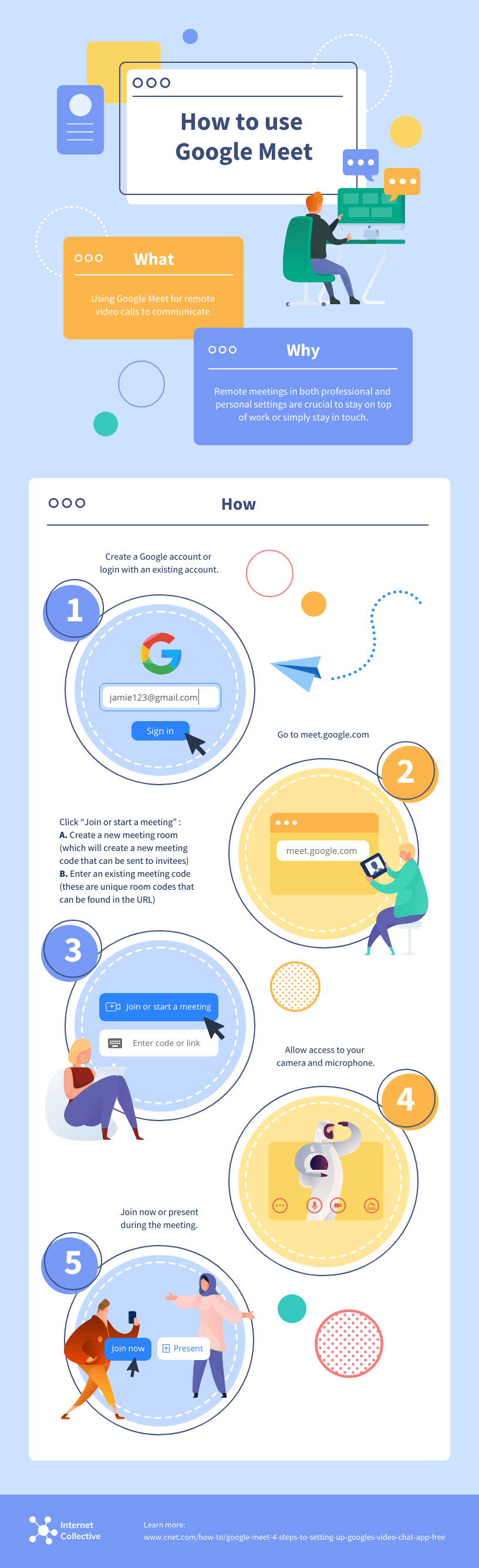
What is the difference between work instruction and SOP?
Work instructions and SOPs both fall under job aids that aim to improve efficiency and quality of work in an organization. However, while they can be similar in structure, work instructions and SOPs have different functions and content.
SOPs summarize the specifications of a process while a work instruction is narrowed down to an individual task and elaborates each of the steps outlined within an SOP.
As you can see, this standard operating procedure provides the different activities and steps involved in the process of training a new employee:
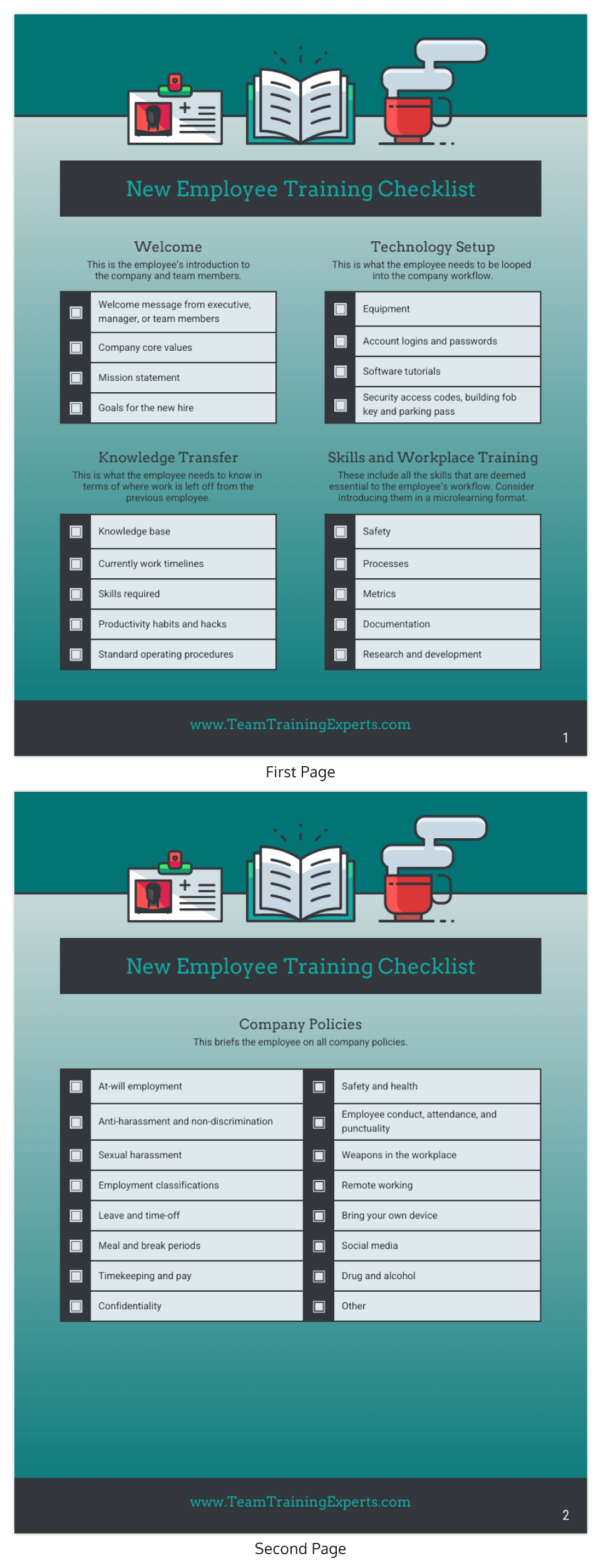
Meanwhile this work instruction discusses each step for onboarding a new employee:
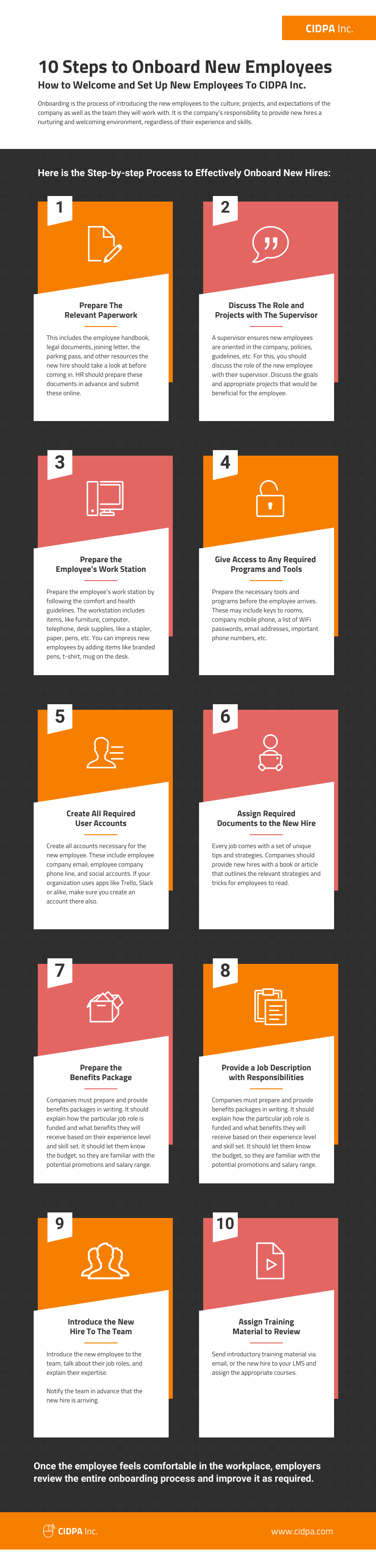
This means the distinction between these documents lies in their use and degree of detail. Work instructions are more applicable for supporting the day-to-day operations of a business while SOPs make processes more systematic from a management standpoint.
In a quality management system, work instructions and SOPs belong in a hierarchy of procedural documents.
At the first level are manuals which serve as a reference point for targets, objectives, and responsibilities. Meanwhile, SOPs and work instructions comprise the second and third levels respectively.
When to use: Work instruction vs SOP
Work instructions are used when establishing a uniform way of doing a task. They are used to show the precise steps for completing a task and often include images, graphics, and illustrations to provide more information and a better demonstration of the steps.
SOPs on the other hand, are used during circumstances that require a standard course of action. They are used to standardize processes and serve as guidelines for routine activities. For example, when managing business email, creating a guide on organizing incoming messages into folders would be an example of work instructions. Meanwhile, using a tool like Clean Email to automate sorting and decluttering could be considered an SOP, as it provides a standardized method for maintaining an efficient inbox.
FAQs about work instructions and SOPs
What is the difference between SOP and OCP?
SOP (Standard Operating Procedure) is a detailed document outlining the steps and processes required to perform a specific task consistently. OCP (Operational Control Procedure) focuses on controlling specific operational aspects to ensure compliance with regulations and standards.
While SOPs provide comprehensive instructions, OCPs are more about maintaining control over specific operations to achieve regulatory compliance.
What’s the difference between policy, procedure, and instruction?
Policies reflect your company values and should govern your business operations in order to influence employee behavior positively.
A procedure then tells people how to put these policies into practice – managers specifically, so they can implement them.
Finally, work instructions specify how to perform specific tasks, which leads to the fruition of policies and procedures.
In conclusion: Work instructions and SOPs both have distinct uses and benefits that can improve business performance
The success of a business will depend on clear, comprehensive, and organized work instructions and SOPs that facilitate the successful execution of business processes and operations.
For actionable work instructions and SOPs, use Venngage to create training materials and take advantage of thousands of fully customizable templates. It’s free to get started.