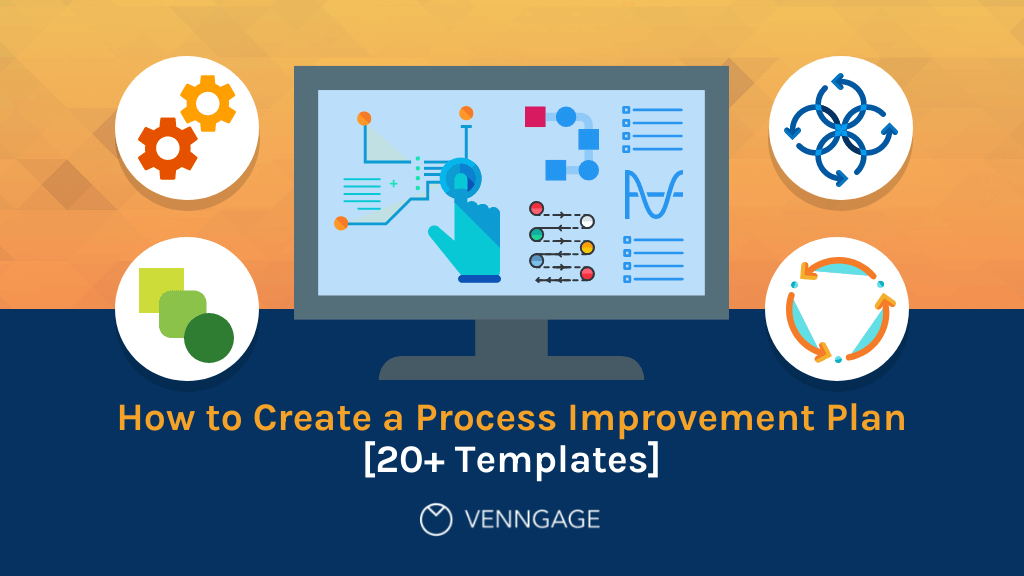
A process improvement plan is a comprehensive and actionable document that outlines the necessary steps to enhance the efficiency, effectiveness and overall performance of processes and procedures within your company. It serves as a roadmap to identify areas of improvement, address bottlenecks, streamline workflows and optimize resource utilization.
By creating a process improvement plan, companies can proactively drive positive change, foster continuous improvement process and achieve higher levels of operational excellence.
Many aspects of process improvement can benefit from visual communication tools like infographics, presentations, mind maps and more. Venngage simplifies process improvement for Learning and Development teams with user-friendly plan templates for efficient implementation and management.
Click to jump ahead:
- How do you create a process improvement plan?
- What are the most common types of process improvement plans?
- What is an example of process improvement?
- Types of process improvement plan & examples
- What are the benefits of establishing a process improvement plan?
- Process improvement plan FAQ
How do you create a process improvement plan?
A well-designed process improvement plan can streamline operations, enhance efficiency and drive organizational growth. To help you navigate this crucial endeavor, here are ten essential steps to create a process improvement plan that yields measurable results:
- Identify the Goals:
Define the specific objectives you aim to achieve through process improvement. For example, reducing customer wait times by 20% or decreasing production errors by 15%.
- Analyze Current Processes:
Thoroughly evaluate existing workflows to identify bottlenecks, inefficiencies and areas of improvement. For instance, examine how information flows between departments or how to improve inventory management.
- Gather Stakeholder Input:
Engage employees, managers and other relevant stakeholders to gather insights and perspectives on process challenges. Example: Conduct interviews or surveys, or integrate a cloud contact center solution to collect feedback on pain points and potential solutions.
- Prioritize Improvement Areas:
Based on the analysis and stakeholder input, prioritize the areas that require immediate attention. This might involve identifying high-impact processes that, when improved, will have a significant positive effect on the organization.
- Set Measurable Objectives:
Establish specific and measurable objectives that align with the identified improvement areas. These objectives should be quantifiable and time-bound. For example, reduce customer complaints by 25% within six months.
- Develop Action Plans:
Create detailed action plans for each improvement area, outlining the steps, responsibilities and timelines for implementing changes. For instance, assign a cross-functional team to streamline the order fulfillment process and develop a timeline for completing the necessary changes. Consider having action plan templates in place so there you team has a framework for how to accomplish processes.
- Implement Changes:
Execute the action plans while closely monitoring progress and ensuring adherence to the established timelines. Example: Introduce new software to automate manual data entry tasks and track key performance indicators. The execution phase is crucial for making sure the improvements are successfully implemented.
- Measure Results:
Regularly measure and evaluate the impact of the implemented changes against the set objectives. This may involve tracking metrics like cost savings, productivity improvements, or customer satisfaction ratings. Monitoring these results will help inform necessary adjustments and future optimization.
- Adjust and Refine:
Based on the results, identify any gaps or areas that need further improvement. Make an adjustment to the action plan accordingly to refine it and continuously optimize the plan as part of the overall improvement process. - Communicate & Engage:
Keep all stakeholders informed about the progress of the process improvement initiatives and encourage their ongoing involvement. Share success stories and celebrate achievements to sustain motivation and engagement.
By adhering to these useful guidelines, you will forge a formidable process enhancement blueprint that propels transformative growth within your organization. Keep in mind that process improvement is an ever-evolving odyssey and constant scrutiny and fine-tuning will safeguard perpetual triumph in fine-tuning your operations.
Process Improvement Plan Case Study
Following the steps we outlined earlier, let’s explore a hypothetical process improvement plan for a doctor’s office that constantly gets complaints from patients about how many forms they have to fill out.
Process Improvement Plan: Reducing Patient Form Burden in a Doctor’s Office
- Identify the Goals:
The goal is to streamline the patient intake process and reduce the number of forms patients have to fill out, resulting in improved patient satisfaction and reduced administrative burden.
- Analyze Current Processes:
Evaluate the existing patient intake process to identify the number and types of forms patients are required to complete, as well as any redundancies or inefficiencies in the process.
- Gather Stakeholder Input:
Engage with patients, front desk staff and healthcare providers to understand their perspectives on form-related challenges and potential solutions. Conduct surveys or hold focus group discussions to gather feedback.
- Prioritize Improvement Areas:
Identify key areas where form reduction can have the most significant impact on patient experience and administrative efficiency. For example, focus on eliminating redundant information across forms or consolidating multiple forms into a single comprehensive document.
- Set Measurable Objectives:
Establish specific objectives, such as reducing the number of forms by 50% within three months, minimizing the time patients spend filling out forms by 25% or achieving a patient satisfaction rating of 80% regarding the form intake process.
- Develop Action Plans:
Create action plans to streamline the patient intake process and minimize form requirements. Examples of actions may include:
- Conduct a thorough review of existing forms and identify areas of overlap or duplication.
- Consult with legal and compliance teams to ensure necessary information is captured while minimizing redundancies.
- Explore the possibility of implementing electronic forms or online pre-registration to expedite the process.
- Train front desk staff on the new streamlined process and educate them on assisting patients in completing forms efficiently.
- Implement Changes:
Execute the action plans by implementing the agreed-upon improvements. This could involve revising and consolidating forms, implementing electronic forms or online pre-registration systems and providing staff training on the revised process.
- Measure Results:
Regularly measure and evaluate the impact of the implemented changes against the set objectives. Track metrics such as the number of forms eliminated, time saved for patients and patient satisfaction ratings related to the revised intake process.
- Adjust and Refine:
Based on the results and ongoing feedback, identify any areas that require further improvement. Refine the process by addressing any remaining pain points or bottlenecks to ensure a seamless and efficient patient intake experience.
- Communicate and Engage:
Maintain open communication with patients, staff and healthcare providers throughout the process improvement journey. Inform patients about the changes and improvements made to the form intake process and encourage their feedback and suggestions for further enhancements.
By implementing this process improvement plan, the doctor’s office can minimize the burden on patients by reducing the number of forms they need to fill out, resulting in improved patient satisfaction and streamlined administrative processes. Remember that continuous evaluation and assessment are essential to adapt to evolving patient needs and ensure ongoing improvements in the patient intake experience.
You can customize this process improvement plan template to reflect the example above:
What are the most common types of process improvement plans?
There are found major methods of process improvement that you may consider integrating into your process improvement plans. Some of these methods are used in the largest companies in the world.
Six Sigma
A quality control method developed by a Motorola engineer, Six Sigma has become a global phenomenon and Six Sigma certification is highly sought-after in many industries. Six Sigma outlines five steps for improving existing business practices, abbreviated to DMAIC:
- Define
- Measure
- Analyze
- Improve
- Control
Here’s how a process improvement plan should be when using the Six Sigma method:
Lean & Lean Six Sigma
Lean traditionally is used by manufacturing companies, but the principles are useful across all industries and as its name suggests, Lean process improvement plans focus on reducing waste. In particular, Lean aims to eliminate any activities that do not add value to the end user of the good or service. The steps are:
- Identify value
- Map value stream
- Create flow
- Establish pull
- Seek perfection
Lean Six Sigma is the hybrid of the two methods, helping organizations improve processes through DMAIC while also eliminating waste.
Total quality management (TQM)
Total quality management (TQM) had its heyday in the 1980s and early 1990s before the advent of Lean and Six Sigma, but its main objectives are still valid today. TQM process development plans focus primarily on quality control, ensuring that the company’s output is of the highest possible quality and determining ways to make output even better.
TQM doesn’t have steps as most other process improvement methods do. Rather, it focuses on principles that should guide an organization with a TQM mindset:
- Customer-focused
- Total employee involvement
- Process-centric
- Full team integration
- Strategic and systemic
- Continuous
- Data-driven decisions
- Constant communication
Plan-Do-Check-Act (PDCA)
Plan-Do-Check-Act (PDCA) is a continuous change management cycle that was first established by engineer and management consultant W. Edwards Deming in the 1950s. Back then it was called a Deming Wheel, which was later modified by Japanese engineers to arrive at its current definition.
The steps involved in PDCA are obvious:
- Plan
- Do
- Check
- Act
What is an example of process improvement?
As the name suggests, process improvement refers to the task of identifying, analyzing and improving existing business processes that are often outdated or no longer efficient enough.
While the term is most often used in a business context, it can refer to any decision or actions that aim to improve a process, be it as simple as finding a shorter route on your drive to work or as complex as improving the whole customer service process of a corporation which might involve investing in a business phone system and training staff, among other things.
Back to its business context, process improvement could target wasteful spending, poor office design, IT system downtime, employee disengagement and many other issues that can doom an organization.
Process improvement can’t be effective without proper process documentation policies in place. If you haven’t documented your company’s processes yet, we can help with that. Check out these process documentation templates to get you started.
There’s more than one type of process improvement plan, which we’ll explore more in detail. In addition to the example we shared above, a process improvement plan can also consist of 6 steps:
Or 4 steps, like this one which is developed using the Plan-Do-Check-Act (PDCA) model:
These steps are, of course, quite simplified and some process improvement plans will require months or years of changes to procedures, hiring practices, training, systems, software and more.
For example, a process improvement plan for a company lacking a specific skill set in its employees can mean hiring new staff and training the existing one. In cases like this, other tools like individual development plans can be useful.
This individual development plan designed for healthcare workers is a good example of how process improvement plans can branch off into other areas.
And once the new process is in place, it’s important to communicate it to the team effectively. That could be through a process infographic, timeline, mind map or other types of visual communication.
Customize this project communication plan to help streamline communication channels between teams working on the same project:
Another example of a process improvement plan, this nursing care plan is used in a healthcare setting only. It could be used to illustrate a new plan aimed at addressing gaps in communication and patient care. But you can use the process suggested in this plan and apply it to any industry.
This creative design process infographic would be an ideal way to share with a creative team a proposed new method of taking clients through the design process. Consider color-coding new or revised steps if creating a piece like this to share a revised company process.
Customize this action plan mind map once you’ve settled on a new process so that team members see steps involved in their tasks but also keep the main objectives in mind.
Types of process improvement plan & examples
Process improvement plans are useful for organizations of all types and their output can include simple verbal instructions. But most companies benefit from creating charts, presentations and infographics to communicate a variety of aspects surrounding the plan.
Check out these process improvement plan templates that may help your organization.
Process improvement plan development examples
Developing a process improvement plan is complicated, but visual tools like infographics can make it easier for your team to grasp the steps involved.
Help your management team and employees understand the steps involved in the project planning, methodology and the plan-do-check-act (PDCA) cycle with this infographic. Customize it for your needs by outlining specific actions they need to take in the bottom section.
This PDCA cycle infographic is ideal for companies that are implementing improvement plans across their organization.
Revised process examples
Once you’ve settled on a new way of doing things, explaining the new process clearly to employees (and sometimes customers) is critical. Process and timeline infographics are helpful, as they allow people to visualize the new steps.
Here’s an example of a process improvement plan to revise customer support process, built based on the PDCA concept:
Customize this project management process infographic for the new process you and your teammates are creating. Quickly change out icons for ones that apply to your business and use My Brand Kit to ensure the design aligns with your corporate identity.
Use this colorful process infographic for a new process that has several steps. Lengthen or shorten as needed to cover all the steps in your revised process. Or use a template like this to create a process improvement project as you begin your work.
Revised policy examples
Process development plans can easily spill over into a variety of business areas and it’s often necessary to craft new policies and procedures on the way to your new process. Infographics and other tools can help you spread the word and document these new policies.
If your new process will require added documentation that needs to be signed by an employee or their supervisor, customize this procedure infographic that explores how to submit expense claims. Change the title, content and illustrations for your needs.
Perhaps your process improvement plan revealed that nobody in your organization is prepared for a disaster or emergency. The output of your process improvement team could be a business continuity plan like this one.
Employee development examples
The success of your new process will depend entirely on your team’s ability to execute it and many organizations find that a major reason why their current processes aren’t working is that team members lack certain skills. So, employee development is often involved in executing a revised plan.
Help team members visualize the skills they need to develop by working with them to create a mind map like this one.
Customize this career planning infographic for team members as you work with them to help them build the necessary skills. While this example is about career planning in general, it’s easy to customize with specifics for your employees.
Change management examples
Humans by nature are resistant to change and your organization may find it challenging to implement a new process. These change management plans may help you communicate and motivate your team.
Follow the steps in this change management process infographic to break through your team’s stubborn adherence to old, inefficient processes.
Update this planning process infographic to help get your team on the side of change. Employees who feel they are involved in steering the company in the right direction will feel a strong sense of ownership in the entire process improvement operation.
What are the benefits of establishing a process improvement plan?
There are many benefits of diving into a process improvement plan in your organization and the most obvious and important is to improve your company’s overall efficiency. Doing so can make the business more profitable in the long run. But that’s not where the benefits end.
The biggest benefits of a process improvement plan include:
- Employee satisfaction: More productive workers make a company more money over time, but they also gain a sense of accomplishment and self-improvement.
- Customer satisfaction: Many process improvement plans target tasks that are customer- or client-facing and making sure your customers are satisfied is crucial for any organization.
- Agility: The business landscape is constantly changing, so putting a process improvement strategy into place will equip your organization to handle future disruption.
- Safety: Efficient processes are helpful to reducing workplace accidents and repetitive stress injuries and examining the physical activities employees are doing as part of their jobs can help make them safer overall.
- Modernization: Organizations that resist technology are likely not long for the world and process improvement plans are ideal for adapting new technologies to your company’s workflows.
- Innovation: In any company, there are things you do because that’s the way you’ve always done them. But breaking those processes down to see how they function is one of the best ways to spark a new idea and create innovation in your organization.
If you’re looking for inspiration on how to visually communicate your improvement strategy, these process infographic examples can help you turn complex workflows into clear, easy-to-follow visuals.
Process improvement plan FAQ
Do you have more questions about creating a process improvement plan for your organization? We’ve got answers.
How do you propose a process improvement plan?
Communication is a critical part of process improvement. If people don’t know or understand why change is needed, it’s unlikely they’ll embrace any new processes. Proposing a process improvement plan requires an individual or small group who will own the plan’s development from start to finish and can be evangelists for the plan across the organization.
What are the contents of a process improvement plan?
In general, process improvement plans must include a definition of the process, an explanation of its steps, an identification of the ways in which it falls short, a proposed new process and a mechanism for monitoring the revised steps.
How do you find areas of process improvement?
If you knew exactly why your organization wasn’t as successful, you’d fix it right away. But finding areas of process improvement means keeping your ear to the ground and observing the organization in an objective way. Common areas of process improvement include authority overlap, constantly missed deadlines, poor quality control, physical safety issues, fixing errors rather than preventing them, employee and customer dissatisfaction and excess spending.
Enhance productivity and eliminate frustration with process improvement plans
Identifying where your company is failing in the processes used across the organization is not an easy task, as it requires dispassionate examination of how you may be falling short. But visual communication tools like infographics, mind maps and process illustrations can help communicate issues to your team and get everyone moving in the right direction.
Interested in visualizing your process improvement plans and gaining buy-in from stakeholders? Start by registering for a FREE Venngage account and choose a suitable process improvement plan to customize. Our templates are professional-looking, fully customizable and really easy to edit, even if you don’t have design experience.